Yesterday, our member Arnold Vaandrager at Vabo Composites published an interesting article about composites in the shipping industry. It is well worth a read and can be found here:
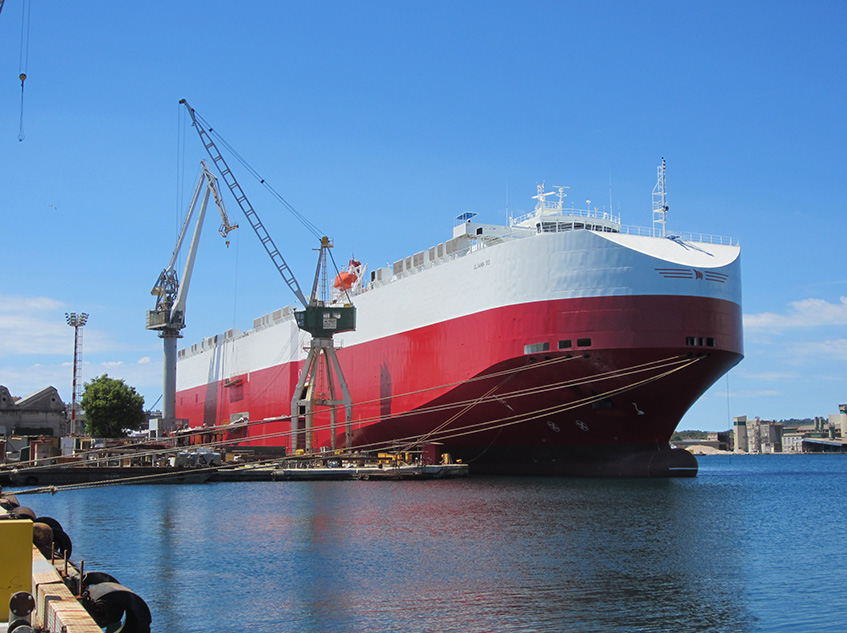
Composites in the shipping industry
Composites in the shipping industry, what are we getting ourselves into? Ships are made of steel! We know how to work with steel and you cannot weld or repair composites yourself. This is why the application and the use of composites is not a conventional choice. Composites however, offer countless advantages, such as their light weight, freedom of shape, acoustic damping, integration of functionality and reduced maintenance. But why then, doesn’t every ship at least use composites on their superstructures?
This same problem occurred earlier when aluminium became an option. Despite the fears and trepidation, aluminium has now become an acceptable material for building ships. Thanks to these experiences, it is now not so much the question of whether composites can be applied, but just a matter of how and to what extent. This will largely depend on the companies who see a competitive advantage in the use of composites and how they will decide to apply it in their designs of ships. This will give them a step up on their competitors. Companies in the past have already gained a leg up by using aluminium and were in the lead at that moment when aluminium became more broadly accepted. Currently, the development of composites is growing at such a high rate that it is certainly worth considering seeing if there is money to be earned. By now we have plenty of evidence in real life to look at. If aeroplanes can be built of composites, it must certainly be possible to build a ship of composites and the more they are applied, the faster the developments in materials and processes will be.
Clear advantages
Proponents of composites will, of course, site the many advantages but the challenges are more than just technical. Challenges also exist as seen from class, market acceptance and especially the business case perspective. If there is no demonstrable advantage in sight, it won’t be much use to start a development of composites products. This is true for every innovation, of course. The other side of the coin is that if no one ever did anything to develop an innovation, we would still be cranking up our cars with handles and have horses in the stable. In other words, a development must be given a fair chance to succeed. It is now generally believed that composites are more expensive than steel, but is that true? Let’s go back to the aluminium example: this is also more expensive than steel but it is still applied everywhere. The explanation is obvious because this material offers many advantages. This can also be said of composites: especially, when we consider that less maintenance is required and greater fuel savings will be realised over the lifespan of a ship.
It’s not only about saving costs but for designers, a whole world opens up when they are given the freedom of shape that composites offer and after all, it’s better to be struck by a door that weighs 35 kilos during bad weather than one that weighs 100 kilos.
Strategic advantage
Perhaps it sounds like it’s better to use composites for everything, but we’re not pretending that composites are the Holy Grail. The material that best suits the design must be selected for every requested application. Today, many composite developments choose to implement a hybrid. This creates a bridge between the world of steel and the world of composites. This is how knowledge and experience are combined to achieve competitive advantages and companies are able to implement innovations.
At this moment it is not very busy in the ship building industry, but we do not expect it to get any worse. So, this is an Ideal moment to take the lead with lightweight materials before the pressure returns. The bicycle is still a good example of innovation – once made of wood, then steel, then aluminium and now carbon (composite). Let’s be honest, the first ships were also made of wood.
So, what are composites anyway?
A composite is a combined material which means, in principle, that multiplex (wood/glue) is also a composite. When we now speak of composites we talk about a combination of fibres with a matrix. These fibres are for example, glass, carbon, aramid and even natural fibres. The matrix holds the fibres together and these most often polyester, vinylester, epoxy (thermosets) or a thermoplastic material. These are just a few examples; experts could expand endlessly on this list. The choice and the composition always depends on the desired application. Even though the composite branch is still considered to be in its beginning, or, in friendlier terms, composites are new materials for application, but this application is not new at all. Over 1000 years ago, people made boats of mud and hay, which is a composite. The list of products that we all know well and perhaps may
not even realise that they are made of composites is infinite: bridges, floodgates, yachts, canoes, tennis rackets, swimming pools, slides, bicycles, roofs, silos, aeroplane landing gears, aeroplanes, car chassis, race cars, refrigerated trailers, spoilers and so on. These products have found their way on the market where money can be earned.
Everyone can use them
To apply a composite, many choices need to be made when it comes to fibres, resins, the number of layers, strengths etc. It may almost seem impossible to make the right choice unless you happen to be an aeroplane designer with a university degree. But that’s not necessarily the case, because when you study the logical use of composites and make the effort of taking a workshop or you follow a course study, anyone with a little know-how can begin working with composites. But, isn’t there an endless list of kinds of steel that can ultimately be used? If you want to use composites, you must focus on utilising the advantages that the materials offer for design. This way, the design itself becomes an advantage. A chicken egg is strong thanks to its shape and how pressure is applied. Other functions such as insulation, paint work, ventilation, acoustic damping, fire-resistance and even ballistics can also be part of the design whereby, the business case can turn out to be more affordable along the way. Or perhaps it’s a good idea to include a piece of the environment of the section that you want to make of composite. Include it in not just the mast, but also in the roof of the wheelhouse or the stairsteps which is particularly difficult to make from steel and in this case, it just might prove advantageous in your financial calculations. These decisions can all be made in the design stage without needing to enlist a “composites expert”. To take it one step further, it is possible to do the basic composite calculations yourself. You can always still hire an expert later who can carry out further calculations layer by layer. Here, it is worthwhile to find out if the barrier is greater than the advantages it can offer.
Come together to strengthen positions
The rising composite branch is still a relatively young industry. Generally, it consists of smaller firms than you would expect in the shipping industry. This does not mean that a wealth of expertise has been acquired which we should certainly tap into. Not only companies, but also organisations such as NLR and TNO have the expertise in house to help with the application of composites. Our universities are quite familiar with the composite phenomenon and this has resulted in more and more college graduates being available who can handle the design aspect. The trend in the branch is slowly but surely developing from individually operating companies towards companies that are coming together to unite forces under one umbrella branch association called CompositesNL (www.compositesnl.nl). Here, education, legislation, internationalisation, innovation regulations and collaborations with other branch associations as NMT (www.maritimetechnology.nl) are addressed. Also, internationally we see an increased number of collaborations and the application of composites is being steadily being simplified. There is E-lass (www.e-lass.eu) where composite companies, classification agencies, universities, accredited testing institutions and big names from the maritime sector come together to implement innovations and try to have changes made to the legislation so that composites can also applied under IMO/SOLAS. The results of this collaboration can already be seen. Besides the developments and innovations mentioned above, it also helps that composite development is being stimulated by local governments which makes it easier to start developments.
Move to lightweight ships that never rust
All in all, with so many developments, composites are on the rise and this is not just for the future. We already can see many examples of the application of composites in the offshore and ship building industries. For example the three top decks on the RoRo ships that are being built by Uljanik in Croatia – all in a composite that is in full compliance with the SOLAS fire requirements. The water bus of Damen is made completely of composites. The composite pipes of Airborne Oil & Gas are applied in the offshore industry and mine sweepers made of composites have been around for forty years. Composite pipe systems already exist on board ships and there are standard composite profiles of Bijl Profielen. Composites are also used for masts, canopies and other parts of superyachts and let’s not forget the certified water tight composite ACCEDOO doors and hatches with fire class by VABO Composites. The list of advantages just keeps on growing both in and outside the shipping industry and this will ultimately result in a mature composites branch with the right volumes and automated production processes. The application of composites is developing rapidly. We can all benefit from this. After all, who wouldn’t want to have lightweight ships that never rust?
I’m a Composite Material
The JEC (www.jeccomposites.com), an institution that represents the development of composites world-wide, has made a beautiful short film on the subject that is certainly worth watching: I’m a Composite Material.
Contact information:
Arnold Vaandrager, VABO Composites
0031527685048, 0031622697121